GENERAL FEATURES
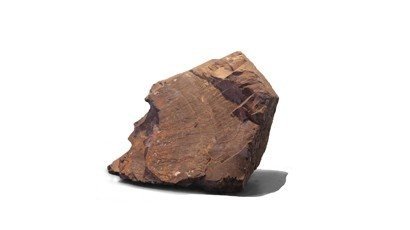
HISTORY
Although it is known that Friedrich Wöhler was the first person to decompose aluminum by mixing anhydrous aluminum chloride with potassium in 1827, it was produced in an impure form by Hans Christian Øersted, a Danish physicist and chemist, about two years ago. Therefore, in the chemistry literature, Øersted's name is mentioned as the person who discovered aluminum. French Henri Saint-Claire Deville developed Wöhler's method in 1846 by using sodium instead of the more expensive potassium. In 1886, the American Charles Martin Hall applied for a patent on the production of aluminum by an electrolytic process, and in the same year the French Paul Héroult developed the same technique in Europe, completely unaware of Hall's discovery. For this reason, the Hall-Heroult process, named after two scientists, is the basic method used all over the world in the extraction of aluminum from its ore today.
KEY FEATURES
Atomic Number: | 13 |
Element Series: | Metals |
Group, Period, Block: | 13, 3, p |
Atomic Weight: | 26.9815386(8) g/mol |
Electron Arrangement: | Ne 3s2 3p1 |
Electrons per Energy Level: | 2, 8, 3 |
PHYSICAL CHARACTERISTICS
State of Matter: | Solid |
Density: | 2.70 g/cm³ |
Liquid Density: | 2.375 g/cm³ |
Melting Point: | 933.47 °K (660.32 °C) |
Boiling Point: | 2792 °K (2519 °C) |
Melting Point: | 10.71 kJ/mol |
Heat of Evaporation: | 294.0 kJ/mol |
Heat Capacity: | 24.2 J/(mol •K) |
ATOM PROPERTIES
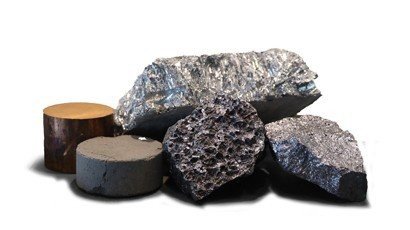
Crystal Structure: | Yüzey merkezli kübik |
Oxidation Level: | (3+) (amfoter oksit) |
Electronegativity: | 1,61 Pauling ölçeği |
Ionization Energy: | 577,5 kJ/mol |
Atomic radius: | 143 pm |
Atomic Radius (calc.): | 118 pm |
Covalent radius: | 118 pm |
OTHER FEATURES
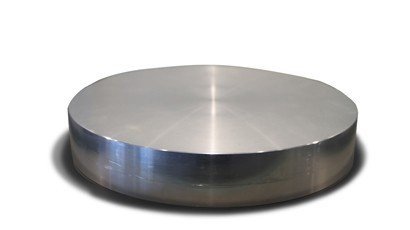
Elektrik Direnci: | 26,50 nΩ•m (20°C'de) |
Isıl İletkenlik: | 237 W/(m•K) |
Isıl Genleşme: | 23,1 µm/(m•K) (25°C'de) |
Ses Hızı: | 5000 m/s (20 °C'de) |
Mohs Sertliği: | 2,75 |
Vickers Sertliği: | 167 MPa |
Brinell Sertliği: | 245 MPa |
ALLOYS
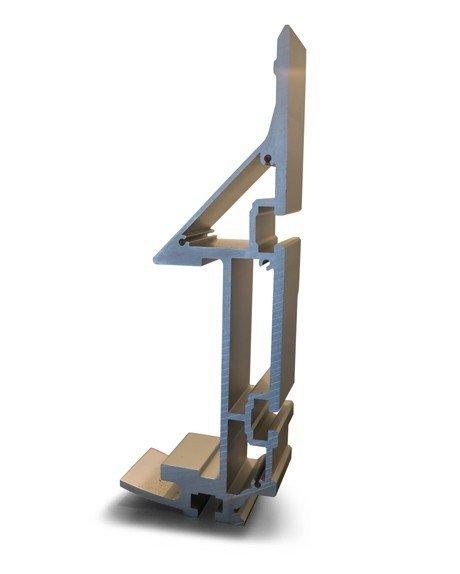
Aluminum alloys are divided into two groups as forging and casting alloys. Plastic deformation capability of forging alloys is very good and can easily be shaped. Heat treatment can be applied to a large portion of the casting and forging aluminum alloys.
According to the American Aluminum Association, aluminum forging alloys are classified with four letters. This classification is as follows:
1XXX: Pure aluminum. Often used in the electrical and chemical industries.
2XXX Al-Cu alloys. Main alloying element is copper. Other alloying elements may also be present, including particularly magnesium; it is used widely in aerospace industry where high strength is required.
3XXX Al-Mn alloys. Main alloying element is manganese. It is used in pipes, tanks and architectural applications.
4XXX Al-Si alloys: Main alloying element is silicon. These alloys have low thermal expansion coefficient and high wear resistance and corrosion resistance. They are used in the production of auto parts, welded structures and plate production.
5xxx Al-Mg alloys: Main alloying element is magnesium. As magnesium ratio increases hardness and strength increase too but the ductility decreases. Because of their high resistance to marine corrosion, they are s used in the manufacture of the structures operated in this environment.
6XXX Al-Mg-Si alloys: Main alloying elements are magnesium and silicon. Shaping property of these alloys is high and often used in the manufacture of the parts produced by extrusion.
7XXX Al-Zn alloys: the main alloying element is copper and magnesium, chromium and zirconium are additional alloying elements. 7XXX series is the one with the highest strength among aluminum alloys. It is used in aircraft parts production and other applications where high strength is required.
8XXX Al-Li alloys: the main alloying element is lithium and tin can also be added. In particular, this material is used in aircraft and space structures and it has good fatigue resistance and good toughness properties. However, compared to other Al alloys it has high production costs.